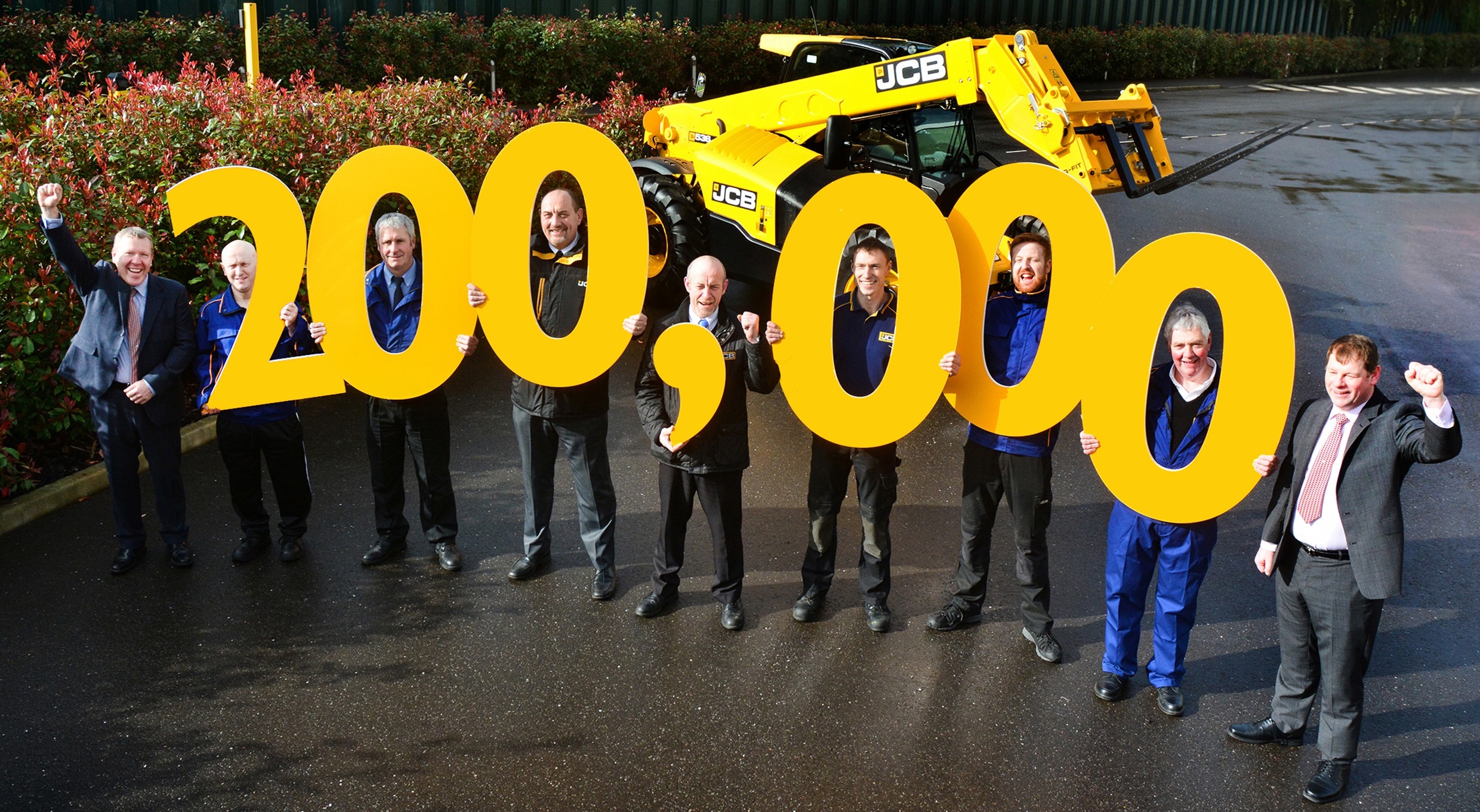
A JCB product that revolutionised the handling of loads on construction sites and farms around the world today passed a major milestone – the production of the 200,000th machine.
The JCB Loadall telescopic handler was first manufactured in 1977, transforming lifting and loading tasks on building sites which until then had been carried out by a small team of men. On farms too the purpose-built machine boosted productivity, stacking bales, loading muck and shovelling grain, replacing rudimentary tractor mounted hydraulic loaders.
The first JCB Loadall – the JCB 520 model – was produced at JCB’s World HQ in Rocester, Staffordshire, on October 3rd, 1977 and in the first full year of production less than 300 machines were made by just a handful of employees. Today thousands of Loadalls roll off the production line every year and the business producing them employs around 800 people.
Today JCB Chairman Lord Bamford said: “From very small beginnings, the JCB Loadall has become a very important machine for JCB and for the construction and agricultural industries. Revolutionary is often a word that is over-used, but in the case of the Loadall it is a perfect description. The way loads are handled on building sites and farms has never been the same since we introduced the Loadall in 1977. The JCB team involved in manufacturing and selling the Loadall is to be congratulated on reaching the production milestone of 200,000 machines.”
JCB employee Richard Jenkinson, aged 62, of, Hilderstone, near Stone has worked for JCB for a total of nearly 40 years and was involved in manufacturing the axles for the very first Loadalls in 1977. He still works for the business producing them today as a Quality Engineer. He said: “I cannot believe it is 39 years since we built the first Loadall and that we have now manufactured the 200,000th machine. It’s an incredible achievement and I am proud to have been involved since day one.”
It took almost 30 years for JCB to sell the first 100,000 Loadalls but it has taken less than 10 for the next 100,000 to be sold – testament to the growing importance of the product and JCB’s strength in this sector. Today JCB is world’s number one producer of telescopic handlers.
When the original 520 model was launched it offered users a rough terrain machine with reach and performance way beyond the capabilities of conventional rough terrain forklifts. Putting the JCB machine out in front was its unique telescopic boom which brought a new solution to the problem of handling materials.
As the machine evolved, its use widened to all areas of the construction sector and the concept quickly spread to agriculture where it is used for a vast variety of tasks from loading grain, stacking bales and towing trailers. JCB today manufactures a total of 90 different Loadall models, 88 of which are manufactured at the World HQ for global markets and two of which are made in India for the domestic market.
One of the major the innovations over the past 39 years has been the introduction of a range of machines with an engine on the side rather than in the centre which enabled the boom to be lowered, improving visibility for operators by 390 mm. In 2008 visibility improvements took another huge leap forward with the introduction of the Hi-Viz range which lowered the boom even further.
The torque lock system introduced on Loadalls in 2001 was also a major milestone because it meant machines could travel quicker on the road and perform much better up hills – as well as improving fuel consumption. The patented Smooth Ride System gave a major boost to users because it improved material retention in the bucket when travelling over rough ground, boosting productivity as well as improving operator comfort.